Project Highlights
Implement Lean across N.American footprint – 8 sites and HQ
Targets: Supply chain, manufacturing, offices, labs
Changeover, capacity, WIP, process standardization, NPD
Coaching, training and change management at all levels
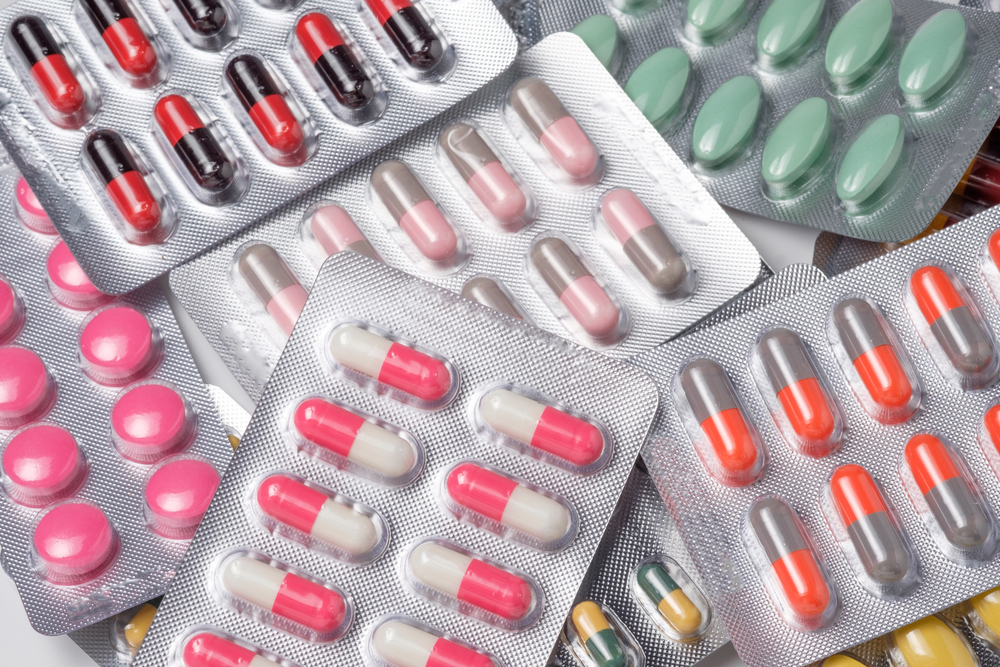
Annualized savings
Faster lab results delivery
Fewer development days
Reduction in total forms
Lean Leaders trained
Lean Leadership Flight Training
Over the years, this client had driven operational improvement efforts with a bottom line focus. Without formal structures and disciplines to drive consistency among their North American locations, sustaining improvement across the company had been difficult.
Kaufman Global was enlisted to deliver their Lean Leadership training program. Phase One consisted of fully enabling thirteen future leaders representing eight sites to apply Lean methods. This phase lasted twelve weeks and included several weeks of classroom training interspersed with eight weeks of on-site improvement activities.
During Phase Two Kaufman worked side-by-side with the participants and site staff to assist them as they applied Lean methods at their home sites. During the project, over 40 rapid improvement events were conducted in a variety of areas including Mold Press operations, Compounding, and Labs. LDMS® was implemented at all sites, resulting in Lean process ownership at the shop floor level.
.
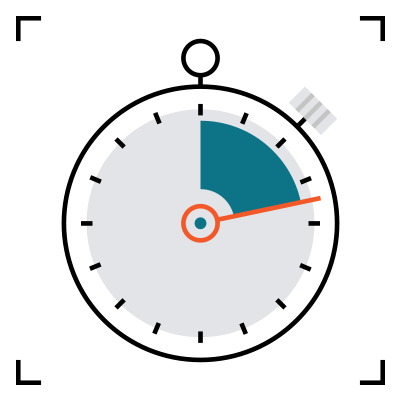
“A year ago we improved our changeover times by 50%, but I was sure that there were other opportunities for even greater improvement. You met the challenge, and by using your Lean tools you squeezed the sponge some more, and have delivered another 50% reduction in cycle time!”
Get Results
Like These.
Real organization change requires fast action, fast impact and enduring confidence in their results. Put Kaufman Global to work for you.